color masterbatch; It is a widely used product in the polymer and plastic industry, and its use is one of the most common methods of producing colored plastic parts in the plastic industry. Color masterbatch, which is also called color concentrate for plastic, consists of two main components: the main color and the carrier polymer resin. In addition to these two components, additives can also be used in color masterbatches.Sometimes, in addition to creating the desired color in the final product, this product also improves and corrects physical and mechanical properties.
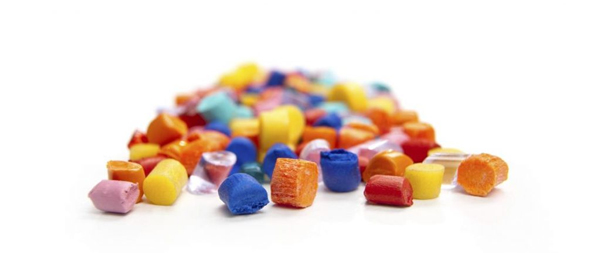
The main purposes of using color masterbatch
Color accentuates the design and delights the eyes. No one can deny the vital role of colors in life. That is why people try to change the appearance of commercial products in terms of color. In the plastic world, color masterbatch is created for this purpose. The use of colored masterbatch granules in the production of products brings vivid and impressive color to plastic products. Of course, in order to have a high quality in these applications, heat resistance, good quality, excellent color dispersion ability, proper light resistance, etc. are necessary.
A masterbatch is usually a combination of a powder and a thermoplastic material. In the industry, in cases where it is necessary to use granules for production, there is a need to add powder materials to the granules. If additive powder is used in pure form, the production environment will be polluted with dust from the powder. For this reason, masterbatch is used in these cases. Now, if we want to produce colored plastic parts, without a doubt, using “Colored Masterbatch” is the best choice. The use of coloring plastics is so prominent and common that in many cases, masterbatch means colored masterbatch.
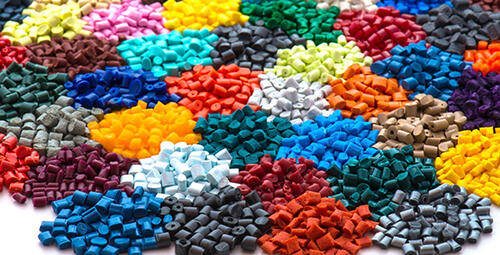
Color masterbatch components
A common misconception in the plastics industry is that color masterbatch is pure pigment. It should be corrected that the pigment is only a part of the color masterbatch and there are two other components besides that. The main components of color masterbatch can be divided into pigment, compatibilizer and carrier polymer:
- Pigments
Including pigments in two groups, organic (such as phthalocyanine green) and inorganic (such as red iron oxide or titanium) and dye, which is like an inert ink or dye and generally cannot be used to dye polyolefin.
- adapter
On the one hand, the presence of compatibilizer causes wetting on the surface of the pigment and as a result, better distribution of the pigment, and on the other hand, without affecting the color quality of the product, it also stabilizes the polymer.
- Carrier polymer
This polymer makes the pigment distribution uniform and makes it easy to form into granules. It is necessary to have the compatibility of the polymer and the dispersing agent, as well as the greater fluidity of the carrier than the pigment and polymer.
Classification of colored masterbatches
Color masterbatches can be categorized based on masterbatch base or masterbatch color.
Based on different polymer bases, the most important masterbatches are:
- Polyethylene color masterbatch
- Color polypropylene masterbatch
- and…
Also, based on the color added to the masterbatch, there are different types of it. The range of different colors can be used in the production of colored masterbatch according to the application of the desired product. It is noteworthy that despite the fact that white and black masterbatches are considered to be colored masterbatches, but due to their great importance in the industry, they are placed in a separate category when classifying masterbatches.
Production process
The color masterbatch production process is usually carried out in two ways, continuous and batch, and generally includes four stages of formulation, feeding, mixing and sieving. The choice of continuous or batch production method is determined according to things such as the degree of automation and production scale. In the continuous mode, the production process is tried to proceed with minimal manual intervention. But in the batch method, the amount of automation is less and there is a need for more manpower. To read more about masterbatch production methods, you can refer to the
masterbatch page.
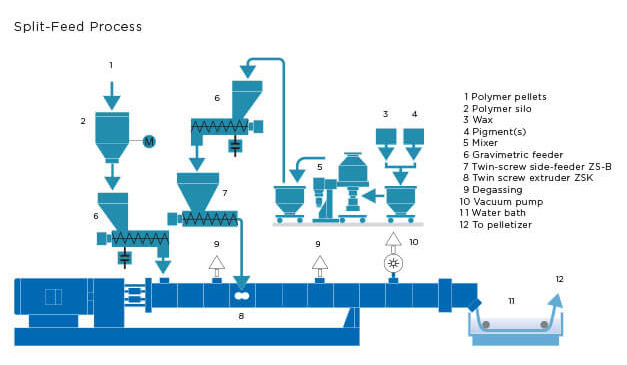
Color masterbatch technical specifications
There are different types of colored masterbatch. The bases of this product are the same different colors with specific codes. According to the customer’s request, the bases can be injected polymer, linear light polymer, etc.; According to the type of products, the customer should choose the base matching and suitable for his production in order to have a better color distribution and blending mode. According to the chemical nature of plastic, you can choose the right color. For example, polyethylene, polypropylene, and PVC can be dyed white (using titanium) or yellow or brown (using chromium oxides), but the colors of blue iron compounds cannot be used in polyethylene and polypropylene formulations. did
According to its melt index, the polymer is selected in such a way that it can dissolve the masterbatch in itself. Since masterbatches are made for a limited number of high-use industrial plastics, it is necessary to provide information about the ability to color plastics with pigments.

The technical characteristics of color masterbatch are: surface transfer resistance, moisture percentage, melting temperature, dispersion in polymer matrix, appearance and polish of color masterbatch, and thermal resistance of the surface are among the characteristics of good color masterbatch. The ease of storage, handling and use due to the granular form of colored masterbatch is one of the advantages of using masterbatch.
Applications
Color masterbatches have different uses. According to the type of product they want to produce and the sensitivity of their work, customers consider one of the different uses of this product. This information about each customer is announced to the customer by Shams Javed in an allocated and customized way. This additive has three main and important uses in the production of plastic materials, which are: producing color, improving properties, and reducing the finished price. The polymer base of this type of masterbatch should usually be similar to the original plastic, and the masterbatch bases are the same as the polymer leasing base. In addition, side additives that improve properties related to spreadability in the extrusion machine. In the following, we mention some of the industrial applications of colored masterbatch:
- Automotive: Color masterbatches are widely used in various internal and external parts of cars.
- Textile: All kinds of fibers have wide applications in modern life. To create a wide range of quality colors, these fibers must contain pigments with light resistance and the ability to withstand air and high dispersion to prevent fabric tearing. A high-quality color masterbatch provides this quality to manufacturers.
- Electronics: Variety of design and color is essential for electronic goods. Masterbatch is used for color variation in most electronic products.
- Toy: Color masterbatch is now used in various industries and businesses using several mediums from textile, automotive, packaging, construction, electronic and electrical, etc.
- Packaging: Color masterbatches are used for a wide range of packaging applications, such as food packaging, etc
Buy colored masterbatch
The packaging of Shams Javaid company’s masterbatches is in the form of 25 kg bags. The information and data sheet of each product is different according to the amount of injection and the percentage of its effective substance. In addition, according to the formula requested by the customer, suggestions are provided to the customer by Shams Javed company. Producers can call 02179615000 (Shams Javaid Arvand Company) to get information about the price of colored masterbatches and to order the product.