Polymer additives or additives are substances that are added in low percentages to various polymers to improve desired properties such as improving processability, increasing thermal resistance, increasing scratch resistance, impact, etc. The molecular weight of polymer additives is lower than that of a polymer, and the percentage of their use in the formulation is very small.
During the process of extrusion or injection of raw materials, due to the high heat and the mechanism of shear stress created on the raw materials, the possibility of destruction and burning of the created polymer is very high, therefore, in order to prevent this situation and also to improve the processability, smoothing, non-sticking of the materials The melt is poured into the extruder, the mold, and the use of polymer additives is inevitable. The uses of these additives in different polymers such as polyamides, polyolefins and polyesters are various, and the percentage used will be different according to each of these components.
How to choose polymer additives
If the production of masterbatch is a specialized work, then the production of polymer additives is a highly specialized matter because it has its own sensitivities and capabilities. One of the reasons for the sensitivity of this issue is the quality test of this product, which cannot be recognized through external components and only in advanced laboratories. It is possible. Considering the cost of these tests, which in turn affects the cost of production, the consumers of this additive tend to buy from reliable manufacturers who provide these products after conducting detailed tests with favorable quality and excellent stability. They offer the market. A quality polymer additive offers significant opportunities to improve the performance of polymer products.
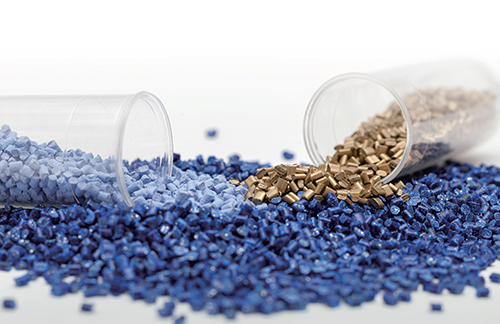
The amount of use of polymer additives
The consumption of polymer additives can vary based on the concentration of additives in the thermoplastic base and based on customer needs. The most important parameter, along with their quality, is the question of its economy. By choosing the right base of raw materials, special mixing plan and using the right equipment, manufacturers can produce a product based on the needs of the market and help the consumer to create the right added value. Some additives have a much higher price than raw materials, so most consumers may not be interested in using these additives at first glance, while the excessive use of some of these products can greatly increase production costs, depreciation. equipment and increase the final quality of the product.
The proper use of polymer additives improves the characteristics of many polymer materials such as durability, hardness, clarity, preventing erosion, etc. Also, the properties of polymers can be significantly changed with suitable additives, and how to use polymer additives is different depending on the type of polymer and its application.
Application of polymer additives
One of the most widely used industries using these additives is the plastic industry. In fact, by changing these materials, it is possible to produce various products such as tires, battery boxes, elastic bands, erasers, etc. Other industries using these additives are as follows
- Production of all kinds of polymer films
- Production of injection and pneumatic parts
- Sack weaving industries
- Packaging industry
- Car parts
- Household appliances
- Electrical appliances
- Industrial parts
- Water and sewer pipes
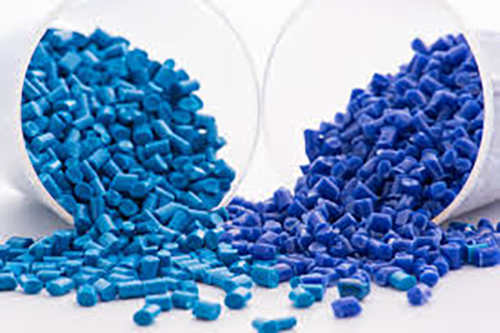
Advantages of using polymer additives
The quality of raw materials and its appropriate distribution in polymer additives, as well as affordable prices, the possibility of regular processing and after-sales services can be factors of a suitable and quality additive. The use of additives can help us greatly in reducing the time, energy and costs of mixing raw materials. Also, due to the lack of proper spreading of some additives, it is not possible to add them directly to the product. For example, in injection processes, adding powder additives is not suitable due to the short length of the device, and instead, it is recommended to use polymer additives.
The importance of polymer additives is so much that today it is practically impossible to design and use polymers, paints and coating systems without using them. Since the beginning of the plastic and paint industry, the application and use of additives to improve processability, flow properties (rheology) and increase the quality of the final product has been necessary and inevitable.
Types of polymer additives
In a comprehensive classification, additives can be divided into the following groups in terms of performance and efficiency:
- fillers
- Lubricants
- Strengthening materials
- Anti-combustion
- Antioxidant
- Antistatic agents
- Anti fog additives
- Additives resistant to ultraviolet rays (Anti UV)
1- Filling additives (fillers)
The set of solid materials with mineral, synthetic and organic base, which are added to the polymer with percentages above 5%, are generally called fillers. The purpose of using fillers is primarily to reduce the price and secondly to improve the physical and mechanical properties.
1-1) Types of fillers
Fillers are basically divided into three categories
- Those that strengthen the polymer and improve the physical and mechanical properties of the polymer.
- Those that only occupy a volume of material so that less polymer is used in making the sample.
- There is also a third type, which is less common, and it is the fillers that are spread in the polymer field to improve the electrical conductivity of the polymer material.
2-1) Characteristics of fillers
Among the characteristics of this additive that affects the properties of polymer materials, the following can be mentioned:
- Increased thermal resistance
- Increased mechanical strength
- Increasing dimensional stability
- Induction of electrical properties
- Increase colorability and surface coverage
- Good weight control
- Hydrophilic or hydrophobic part
According to the definition of fillers, air can be introduced as the cheapest filler used in the production of foams, which makes the piece lighter and reduces its final price.
2- Lubricants
Lubricants are additives that reduce the attraction and friction between the hot surfaces of the forming devices and the surface of the molten polymer. This additive reduces the coefficient of friction between the film layers or the film with any other surface that is in contact with it and causes better and easier separation of the film from the surface. The purpose of this action is not to damage the device and products during the process.
1-2) Types of lubricants
In short, lubricants are classified into two groups in terms of performance:
Internal Lubricant:
The use of these lubricants is to reduce the friction between molten polymer materials and by eliminating the intermolecular forces between the polymer chains, they reduce their viscosity so that the production process can be done easily. In fact, these materials help to facilitate the flow of molten material by reducing the viscosity of the molten material. For example, the internal lubricants used for PVC must be compatible with PVC so that they do not come out of the polymer mixture due to the increase in heat and pressure.
External Lubricant:
An external lubricant is used to reduce the contact and friction of the molten plastic with the hot surfaces of the devices. The external lubricant must be in such a way that it is not compatible with the raw material so that it can come out of the machine and cover the external surface of the product. The external lubricant that is used in the polymer mixture works in such a way that it melts at the temperature of the process and reaches the contact surface of the part and the mold and protects the part from direct contact with the mold and from sticking to it.
2-2) chemical compounds of lubricants
Lubricants are generally organic compounds that are divided into the following groups:
- Fatty alcohols
- Acid esters (Dicarboxylic acid ester)
- Fatty acids
- Acid-amides
- Metallic soaps such as stearates
- Esters
- Oxidized polyethylene waxes
- Polyethylene waxes
- Paraffin waxes
2-3) Characteristics of lubricants
Lubricants are added to the polymer mixture in small amounts in solid, powder or liquid form. The amount of lubricant in the formulation is between 0.25 and 1%, which depends on the forming machine and the final appearance of the desired part.
The effectiveness of a lubricant depends on the extent to which the particles are dispersed throughout the part and absorbed by the polymer product.
For example, a small amount of a lubricant causes high viscosity and destruction of the molten polymer material, which is due to the attraction between molecules, as well as the tension between the mixture and the hot surface of the device, and on the other hand, a strong increase in the lubricant causes the polymer material to be very slippery. And production decreases. Of course, the condition of the compatibility of the lubricant with the polymer material must be met in this process.
Other benefits of using lubricants include the following:
- Creating a shiny appearance
- Good separation from the mold
- Anti-blocking (preventing polymer layers from sticking together)
- Reduce process equipment slowdowns
3- Strengthening additives
Polymer additives that strengthen their mechanical or thermal properties by adding them to polymers are called reinforcing additives. The mechanism of the effectiveness of these materials is to create strong interactions with the polymer and thus improve the properties of the polymer. Usually, to create a strong interaction between the reinforcing agent and the polymer material, methods such as surface modification of the filler or the use of compatibilizing agents are used. Among the most famous reinforcing fillers are glass fibers, carbon black, carbon fibers, glass powder, nanoparticles, wollastonite and natural fibers.
4- Antioxidant additives
Polymer products usually lose their initial strength when exposed to oxygen, and after a while, oxygen causes the products to age and reduce their quality and become opaque. This additive prevents oxidation and reduces the adverse effects of oxygen on polymer products.
5- Antistatic additives (anti-static)
Static electricity may occur due to collision of plastic parts during transportation or wear of polymer materials with additives during production. This static electricity provides the possibility of absorbing dust and suspended particles in the air, in addition to this, there is also the possibility of accidents such as fire or electrocution of workers. The mechanism of this additive is such that by creating a layer on polymer products, it will prevent the production of electricity and the occurrence of such incidents.
6- Clarifying additives
Cleaning the cylinder, mandrel and other parts of polymer production machines is a very time-consuming task, so this work is done faster by using this additive. This additive is able to clean the machine from the previous materials and colors to prepare the machine for the production of the next products.
7- Polishing additives
The appearance of products is important for every customer. This additive is able to give transparency and a special effect to the manufactured products and also improve their appearance.
8- Anti-fog or anti-dew additives
One of the challenges in the field of using polymer films is the production of fog (or dew). The cause of fog formation is the condensation of water vapor on the surface. In greenhouse films or food packaging, this phenomenon is more likely due to high humidity. These droplets are formed on its surface due to the difference in the surface tension of water with the non-polar polymer forming the film.
To solve this problem, manufacturers use anti-fog additives in the formulation of polymer films. The anti-fog additive is mainly used as a masterbatch in the composition and formulation of the film.The concentration of this additive decreases over time due to migration to the surface and its tendency to dissolve in water, thereby weakening its performance. For this reason, producers of polymer films should consider the optimal amount of this additive in their formulation design.
9- Anti-UV additives
Anti-UV materials, which are known as ultraviolet light absorbers (UV) or ultraviolet light stabilizers, are one of the most widely used polymer additives in the production of injection and extrusion products of polyolefins, including PP and PE, such as thin films, normal and thick films, films Agriculture, sacks, jumbo, polymer sheets, especially plastic cartons, fibers and polymer pipes and joints are used to increase the life of plastic parts in the outdoor environment, prevent yellowing, discoloration and fading in the sunlight, and as a result The stability and resistance of polymer products are more in atmospheric conditions.
Frequently asked questions
- Do all polymer products need additives? No, not all polymer products require polymer additives. The use of polymer additives depends on the type of product, required properties and specific applications. Some polymers are capable of providing suitable properties on their own, while in other cases, polymer additives can provide improved or additional properties.
- Is it harmful to use additives? Detergent additives are generally safe to use because they are typically designed for use in household and commercial products. However, in case of sensitivity or allergy to some ingredients, before use, it is better to read the signs and instructions of the manufacturer and consult a doctor if necessary.
- Which lubricant is the best?The best lubricant for you depends on the type of material you are going to wash or clean. Each type of material has its own characteristics and needs, and based on them, you should choose the best lubricant.